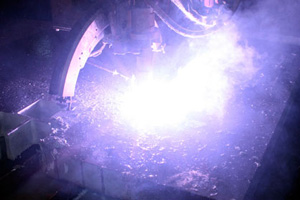
Plasma gouging, or plasma arc gouing, is a subset of the more popularized plasma cutting approach to metal profiling. While it is a lesser known method, plasma gouging and plasma cutting share many advantages. These include:
There are four types of gouging processes, including plasma arc gouging. The other three are known as:
-
Mechanical Gouging
-
Oxyfuel Gouging
-
Air Carbon Arc Gouging
Mechanical gouging includes the processes of grinding, chipping, routing, and hand miling. Oxyfuel gouging is an alternative method of oxyfuel welding and cutting. It is a thermal or chemical approach where the metal is heated using fuel gas, to the point where it is capable of igniton. A jet of oxygen has is then used to burn (cut) the fuel gas are of the metal. Air carbon arc gouging creates a groove / gouge by joining the tip of a carbon electrode and the metal to be cut, creating an electrical arc. A powerful flow of air around the tip is created, essentially blowing away the metal.
Plasma gouging employs the same process as plasma cutting. The methods differ in the type of torch they require.
In plasma cutting systems, a highly pressurized inert gas flows through an extremely narrow passage that contains a negatively charged electrode. Additionally, the gas passes through the swirl ring, causing it to create a swirling flow pattern, increasing energy. The nozzel touches the metal workpiece, powering the negative electrode and creating a plasma arc that heats the gas to a state of plasma.
The flow of extremely hot and pressurized plasma is protected by shiedling gas that surrounds it. The shiedling has ensures the direction of the plasma beam. The gouging process also makes use of shielding gas.
The main purpose of plasma arc cutting is to create a straight edge cut from narrow kerfs (slits or grooves), while also producing very little dross (metal slag).
The main purpose of plasma arc gouging is to increase the volume of metal removal as much as possible. Therefore, the torch of a plasma gouger creats a much wider and softer arc, as opposed to the restrained and thin arc found in the torch of a plasma cutter.
Plasma grougers began as a device for weld preparation and removal. Then, and even today, the machine is used to increase the strength of materials and eliminate defects. Examples of the types of defects it removes are:
Industrial uses of plasma gouging are similar to those of plasma cutting. These include the manufacturing and repair of:
Plasma gouging is also used in any instance needing removal of excess metal, extra weld, and any defects detected on the workpeice. Depending on the goal of the cutting process, plasma gouging is a great variation to plasma cutting. Plasma gouging is very easy to use, and is capable of high processing speeds. Moreover, the cost of operation is considered reasonable within the industry. If requiring a metal cutting process to edit previous errors, and / or improve strength, plasma gouging should be highly considered.